How Much Does A Train Car Weigh? Join CARS.EDU.VN as we delve into the fascinating world of rail transport to uncover the weights of train cars, examining factors influencing their mass and benefits. Understand how rail transport contributes to a greener future by exploring weight considerations and the intricacies of train car design.
1. Understanding Train Car Weight: An Overview
When discussing rail transport, a common question arises: How much does a train car weigh? The answer isn’t straightforward, as train car weight varies considerably based on type, construction materials, and intended cargo. This section provides an overview of the typical weights of different train cars and the factors that influence them.
- Types of Train Cars: The rail industry utilizes a variety of car types, each designed for specific cargo. Common types include:
- Boxcars: Enclosed cars for general freight.
- Flatcars: Open cars for oversized or irregularly shaped items.
- Tank Cars: Designed for transporting liquids and gases.
- Hopper Cars: Used for bulk commodities like coal and grain.
- Autoracks: Specialized for transporting vehicles.
- Typical Weight Ranges: While exact figures vary, here’s a general idea of train car weights:
Train Car Type | Empty Weight (tons) | Loaded Weight (tons) |
---|---|---|
Boxcar | 25-30 | 70-100 |
Flatcar | 20-25 | 60-90 |
Tank Car | 25-35 | 80-120 |
Hopper Car | 20-30 | 80-110 |
Autorack | 30-40 | 60-80 |
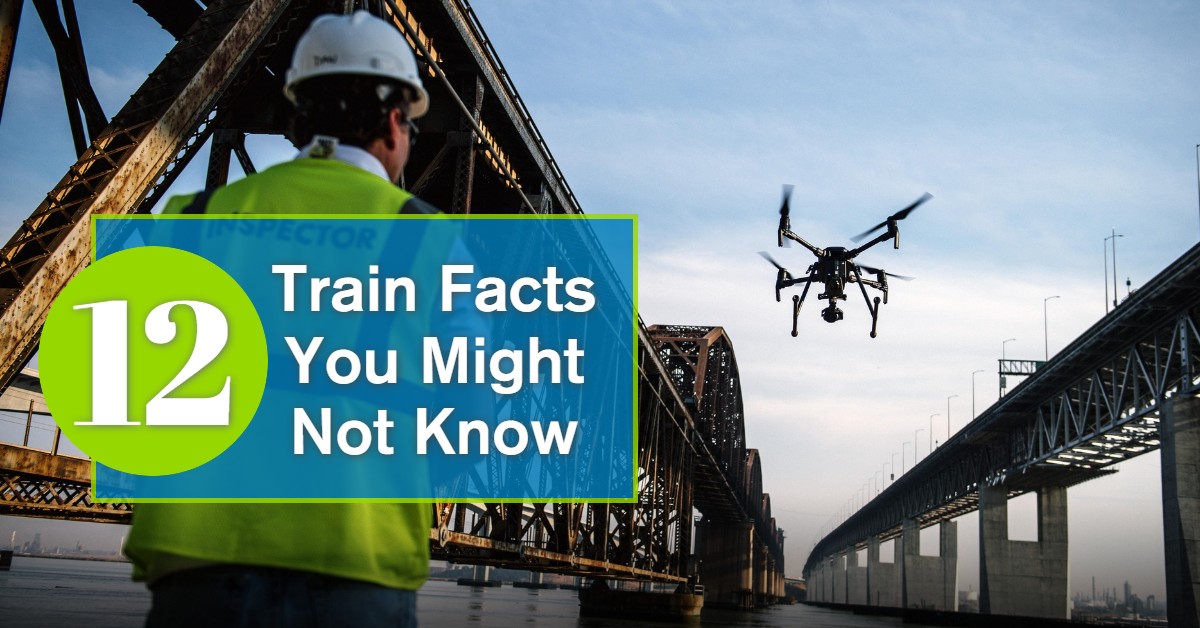
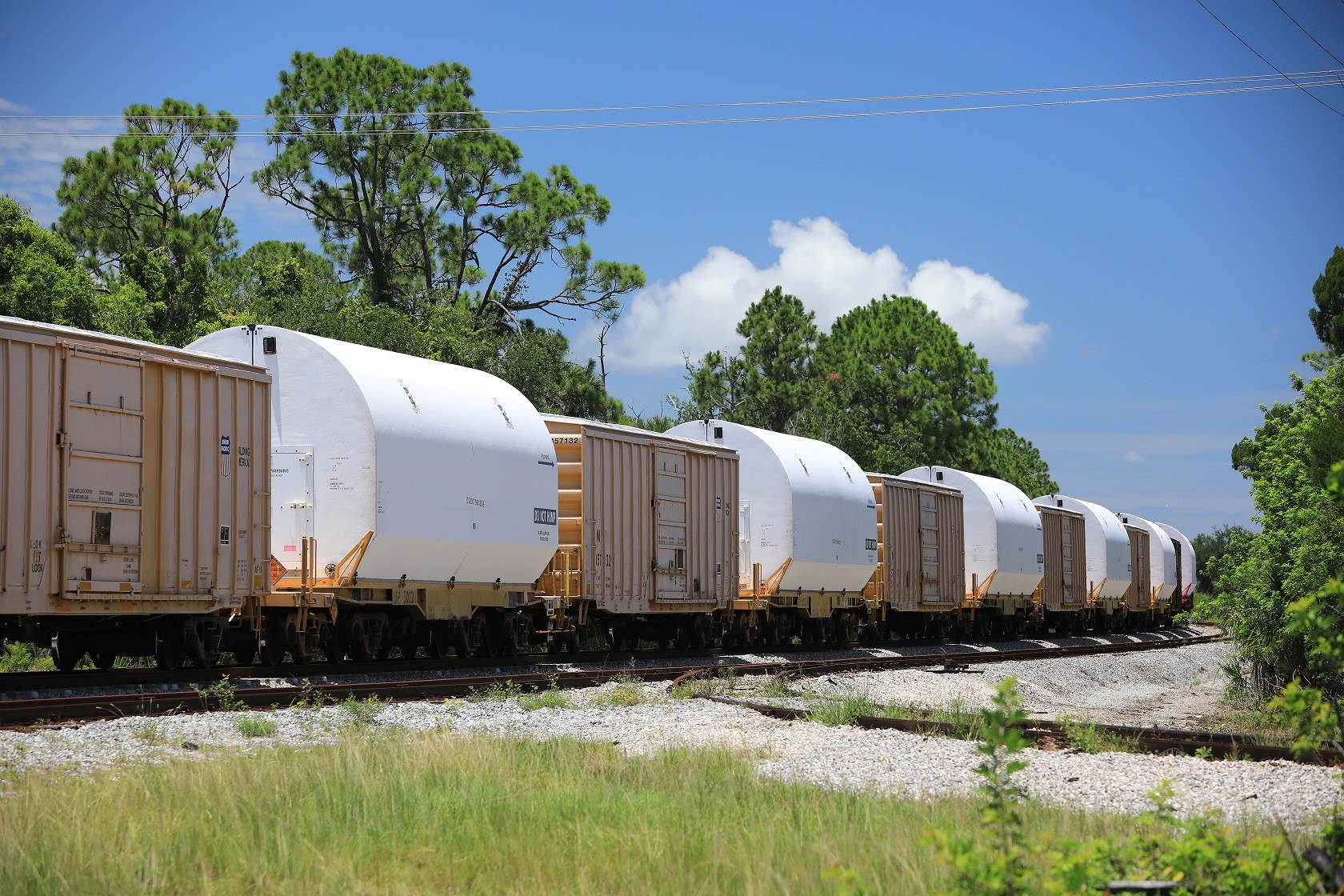
- Factors Influencing Weight: Several factors contribute to the weight of a train car:
- Construction Materials: Steel is the primary material, but variations in thickness and grade impact weight.
- Car Design: The specific design, including length, height, and any specialized features, affects the overall weight.
- Intended Cargo: Cars designed for heavier cargo are built with stronger, heavier materials.
- Regulations and Standards: Safety regulations and industry standards dictate minimum strength and construction requirements, influencing weight.
1.1 Benefits of Understanding Train Car Weight
Knowing how much a train car weighs provides several benefits:
- Optimized Loading: Understanding weight limits ensures safe and efficient loading practices.
- Infrastructure Planning: Weight data is crucial for designing and maintaining rail infrastructure, including bridges and tracks.
- Fuel Efficiency: Weight impacts fuel consumption, making it a key consideration for optimizing train operations.
- Safety: Adhering to weight limits is essential for preventing derailments and other accidents.
CARS.EDU.VN is your go-to source for in-depth information on rail transport, including train car weights and their significance.
2. The Weight of Different Types of Train Cars
Diving deeper into the question, “How much does a train car weigh?,” this section explores the specific weights of different types of train cars. We will examine the typical empty and loaded weights, along with the design features that contribute to these figures.
2.1. Boxcars
Boxcars are general-purpose freight cars designed to carry a wide variety of goods. They are fully enclosed to protect cargo from the elements.
- Typical Empty Weight: 25-30 tons.
- Typical Loaded Weight: 70-100 tons.
- Design Features: Boxcars feature sturdy steel frames and walls, with doors on the sides for loading and unloading. The weight varies based on the car’s length and the thickness of the steel used.
2.2. Flatcars
Flatcars are open, flat-decked cars used for transporting oversized or irregularly shaped items such as machinery, vehicles, and construction materials.
- Typical Empty Weight: 20-25 tons.
- Typical Loaded Weight: 60-90 tons.
- Design Features: Flatcars have a simple, robust design with a reinforced steel deck. They often include tie-down points for securing cargo. The absence of walls and a roof contributes to their lighter empty weight compared to boxcars.
2.3. Tank Cars
Tank cars are specialized for transporting liquids and gases, ranging from petroleum products to chemicals and food-grade materials.
- Typical Empty Weight: 25-35 tons.
- Typical Loaded Weight: 80-120 tons.
- Design Features: Tank cars consist of a cylindrical tank mounted on a steel frame. The tank is designed to withstand high pressures and may include insulation or heating systems, adding to the overall weight.
2.4. Hopper Cars
Hopper cars are used for transporting bulk commodities like coal, grain, and minerals. They feature sloped bottoms that allow for easy unloading.
- Typical Empty Weight: 20-30 tons.
- Typical Loaded Weight: 80-110 tons.
- Design Features: Hopper cars have a sturdy steel construction with multiple hoppers for efficient unloading. The weight depends on the car’s capacity and the thickness of the steel used in its construction.
2.5. Autoracks
Autoracks are specialized cars designed to transport vehicles. They can be enclosed or open, with multiple levels to maximize capacity.
- Typical Empty Weight: 30-40 tons.
- Typical Loaded Weight: 60-80 tons.
- Design Features: Autoracks feature a multi-level structure with ramps and tie-down systems to secure vehicles. Enclosed autoracks have side panels and a roof to protect the vehicles from damage during transit, increasing their weight.
**2.6. Locomotive
Locomotives are the powerhouse of the train.
- Typical Empty Weight: 190-215 tons.
Understanding the weight variations among different train car types is crucial for efficient and safe rail operations. For more detailed information, visit CARS.EDU.VN.
3. Factors Influencing the Weight of a Train Car
Several key factors influence how much a train car weighs. Understanding these elements is vital for optimizing rail transport and ensuring safety. This section examines the primary factors affecting train car weight.
3.1. Construction Materials
The materials used in constructing a train car significantly impact its weight.
- Steel: The primary material for most train car components, including the frame, walls, and undercarriage. The type and thickness of the steel determine the car’s strength and weight. High-strength steel alloys are used in some cases to reduce weight while maintaining structural integrity.
- Aluminum: Used in some specialized cars to reduce weight, improving fuel efficiency and increasing payload capacity. Aluminum is lighter than steel but may not be suitable for all applications due to its lower strength and higher cost.
- Composite Materials: Increasingly used in interior components and some structural elements to reduce weight and improve corrosion resistance.
- Wood: Historically used in boxcar construction, wood is now primarily limited to flooring and interior linings.
3.2. Car Design and Size
The design and size of a train car directly affect its weight.
- Length and Height: Longer and taller cars require more material, increasing their weight.
- Frame Structure: The design of the car’s frame and undercarriage impacts its strength and weight. Reinforced frames are necessary for heavier loads.
- Specialized Features: Features like refrigeration units, heating systems, and loading mechanisms add to the overall weight.
- Aerodynamics: Aerodynamic designs can reduce drag, improving fuel efficiency. These designs may add slightly to the weight but offer long-term benefits.
3.3. Load Capacity and Regulations
The intended load capacity and regulatory requirements play a crucial role in determining train car weight.
- Maximum Load: Cars designed to carry heavier loads require stronger, heavier materials.
- Safety Standards: Regulations such as those set by the Association of American Railroads (AAR) dictate minimum construction standards to ensure safety. These standards influence the type and amount of material used, affecting weight.
- Axle Load Limits: Regulations limit the maximum weight per axle to prevent damage to tracks and bridges. This limit influences the design and weight of the car.
- Impact Resistance: Cars must be designed to withstand impacts and collisions, requiring robust construction and adding to the weight.
3.4. Technology and Added Features
Technological advancements and added features can also influence train car weight.
- Braking Systems: Modern braking systems, such as electronically controlled pneumatic (ECP) brakes, improve safety and efficiency but add weight.
- Monitoring Systems: Sensors and monitoring equipment provide real-time data on car performance, but these systems contribute to the overall weight.
- Suspension Systems: Advanced suspension systems improve ride quality and reduce wear on tracks and equipment. These systems can add weight but also extend the lifespan of the car.
- Insulation: Insulated cars, such as those used for transporting temperature-sensitive goods, have additional weight due to the insulation materials.
Understanding these factors provides a comprehensive view of how train car weight is determined. For further insights and detailed specifications, visit CARS.EDU.VN.
4. How Train Car Weight Impacts Efficiency and Safety
The weight of a train car significantly impacts both the efficiency and safety of rail transport. Understanding these impacts is crucial for optimizing operations and ensuring a safe environment. This section explores the relationship between train car weight and key operational considerations.
4.1. Fuel Consumption and Energy Efficiency
- Increased Weight, Increased Fuel: Heavier train cars require more energy to move, leading to higher fuel consumption.
- Optimizing Load Distribution: Proper load distribution and weight management can minimize fuel consumption.
- Lightweight Materials: The use of lightweight materials, such as aluminum and composites, can reduce the overall weight of the car, improving fuel efficiency.
- Aerodynamic Design: Aerodynamic designs can reduce drag, further improving fuel efficiency.
- Idling Reduction Technologies: Technologies that reduce idling time and optimize engine performance can help mitigate the impact of heavy train cars on fuel consumption.
- According to the Association of American Railroads (AAR), railroads are three to four times more fuel-efficient than trucks on a ton-mile basis.
4.2. Infrastructure and Maintenance
- Wear and Tear: Heavier train cars cause more wear and tear on tracks, bridges, and other infrastructure.
- Maintenance Costs: Increased wear and tear lead to higher maintenance costs and more frequent repairs.
- Track Design: Track design and construction must account for the maximum weight of train cars to ensure safety and longevity.
- Bridge Capacity: Bridges must be capable of supporting the weight of fully loaded train cars. Regular inspections and maintenance are essential to prevent failures.
- Optimized Routes: Careful route planning can minimize stress on infrastructure by avoiding routes with weak bridges or tracks.
4.3. Safety Considerations
- Derailment Risk: Overloaded or improperly loaded train cars increase the risk of derailment.
- Braking Performance: Heavier train cars require longer stopping distances, impacting braking performance.
- Load Securement: Proper load securement is essential to prevent shifting or falling cargo, which can lead to accidents.
- Speed Limits: Speed limits are often reduced for trains carrying heavy loads to minimize the risk of accidents.
- Inspection Protocols: Regular inspections are crucial for identifying and addressing potential safety issues related to train car weight and load distribution.
4.4. Operational Efficiency
- Load Capacity Optimization: Maximizing the load capacity of train cars while staying within weight limits is essential for operational efficiency.
- Turnaround Time: Efficient loading and unloading processes can reduce turnaround time and improve overall efficiency.
- Real-Time Monitoring: Real-time monitoring systems provide valuable data on train car weight and performance, allowing for proactive adjustments to optimize operations.
- Data Analytics: Data analytics can be used to identify trends and patterns related to train car weight and performance, helping to improve efficiency and safety.
- Route Optimization: Optimizing routes based on train car weight and infrastructure conditions can improve efficiency and reduce fuel consumption.
Understanding the impact of train car weight on efficiency and safety is vital for optimizing rail operations. CARS.EDU.VN offers comprehensive resources and expert advice to help you navigate these complex issues.
5. Innovations in Train Car Design for Weight Reduction
To improve efficiency and reduce environmental impact, innovations in train car design are focused on reducing weight. This section explores several key innovations aimed at achieving this goal.
5.1. Advanced Materials
- High-Strength Steel: Using high-strength steel alloys allows for thinner, lighter components without sacrificing structural integrity.
- Aluminum Alloys: Aluminum alloys offer a significant weight reduction compared to steel, particularly in car bodies and frames.
- Composite Materials: Composite materials, such as carbon fiber reinforced polymers (CFRP), are increasingly used in non-structural components to reduce weight and improve corrosion resistance.
5.2. Optimized Structural Design
- Finite Element Analysis (FEA): FEA is used to optimize the design of train car structures, ensuring maximum strength with minimal material.
- Topology Optimization: This technique identifies the most efficient material distribution for a given load, resulting in lighter and stronger designs.
- Modular Design: Modular designs allow for the use of standardized components, reducing weight and simplifying manufacturing.
5.3. Aerodynamic Improvements
- Streamlined Car Bodies: Aerodynamic car bodies reduce drag, improving fuel efficiency and reducing the energy required to move the train.
- Gap Sealing: Sealing gaps between cars reduces air turbulence, further improving aerodynamics.
- Fairings and Spoilers: These devices can be added to train cars to optimize airflow and reduce drag.
5.4. Lightweight Components
- Lightweight Braking Systems: Advanced braking systems using lightweight materials and innovative designs reduce the overall weight of the car.
- Optimized Suspension Systems: Suspension systems designed for weight reduction improve ride quality and reduce wear on tracks and equipment.
- Lightweight Interior Components: The use of lightweight materials in interior components, such as flooring and panels, can further reduce the overall weight of the car.
5.5. Energy-Efficient Technologies
- Regenerative Braking: This technology captures energy during braking and stores it for later use, reducing the overall energy consumption of the train.
- Solar Panels: Solar panels can be integrated into train cars to provide auxiliary power, reducing the load on the main engine and improving fuel efficiency.
- Smart Sensors and Monitoring Systems: These systems provide real-time data on train car performance, allowing for proactive adjustments to optimize energy consumption and reduce weight-related stress.
By implementing these innovations, train car manufacturers can significantly reduce weight, improving efficiency, reducing environmental impact, and enhancing the overall performance of rail transport. Stay informed about the latest advancements in train car design at CARS.EDU.VN.
6. The Role of Regulations and Standards in Train Car Weight
Regulations and standards play a critical role in governing train car weight, ensuring safety, and promoting interoperability within the rail industry. This section examines the key regulations and standards that influence train car weight and design.
6.1. Association of American Railroads (AAR)
- Standards and Recommended Practices: The AAR establishes standards and recommended practices for train car design, construction, and maintenance. These standards cover various aspects, including weight limits, materials, and structural integrity.
- Interchange Rules: The AAR’s interchange rules govern the interchange of train cars between different railroads, ensuring that cars meet specific safety and performance standards.
- Rule 88: Rule 88 of the AAR Interchange Rules addresses the maximum gross weight on rail (MGWR) for freight cars. It specifies the allowable weight based on axle load, influencing the design and construction of train cars.
- The AAR’s standards are crucial for maintaining the safety and efficiency of North American rail transport.
6.2. Federal Railroad Administration (FRA)
- Safety Regulations: The FRA is responsible for enforcing safety regulations related to rail transport in the United States. These regulations cover various aspects of train car design, construction, and operation.
- Track Safety Standards: The FRA’s track safety standards specify the requirements for track geometry, strength, and maintenance, which influence the maximum allowable weight of train cars.
- Equipment Safety Standards: The FRA establishes equipment safety standards for train cars, including requirements for braking systems, couplers, and other critical components.
- The FRA’s regulations are essential for ensuring the safety of rail transport and protecting the public.
6.3. International Standards Organization (ISO)
- ISO Standards for Freight Containers: ISO standards for freight containers specify the dimensions, weight, and strength requirements for intermodal containers used in rail transport.
- ISO 668: This standard defines the classification, dimensions, and ratings of freight containers, influencing the design and weight of train cars used to transport these containers.
- ISO 1496: This standard specifies the testing requirements for freight containers, ensuring that they meet specific safety and performance standards.
- ISO standards promote interoperability and efficiency in global rail transport.
6.4. Other Regulatory Bodies
- Transport Canada: In Canada, Transport Canada is responsible for regulating rail transport, establishing safety standards and regulations for train car weight and design.
- European Union Agency for Railways (ERA): In Europe, the ERA sets standards and regulations for rail transport, including requirements for train car weight and interoperability.
6.5. Impact on Train Car Weight
- Weight Limits: Regulations and standards establish maximum weight limits for train cars, influencing the design and materials used in their construction.
- Safety Requirements: Safety regulations dictate minimum strength and performance requirements for train car components, affecting their weight.
- Interoperability: Standards promote interoperability by ensuring that train cars meet specific weight and dimension requirements, allowing them to be used on different rail networks.
Compliance with regulations and standards is essential for ensuring the safety and efficiency of rail transport. CARS.EDU.VN provides comprehensive information on these regulations and standards, helping you stay informed and compliant.
7. Calculating the Weight of a Train Car
Knowing how to calculate the weight of a train car is essential for ensuring safe and efficient operations. This section provides a step-by-step guide to calculating both the empty weight (tare weight) and the loaded weight (gross weight) of a train car.
7.1. Understanding Key Terms
Before calculating train car weight, it’s important to understand the following terms:
- Tare Weight: The weight of an empty train car, without any cargo.
- Load Limit: The maximum weight of cargo that a train car is designed to carry.
- Gross Weight: The total weight of a train car, including both the tare weight and the cargo weight.
- Axle Load: The weight distributed on each axle of the train car. Regulations often limit the maximum axle load to prevent damage to tracks and bridges.
7.2. Finding the Tare Weight
The tare weight of a train car is usually marked on the car itself. Look for a label or plate that indicates the “LT WT” (light weight) or “TARE” weight. This value is typically given in pounds or kilograms.
- Example: A boxcar has a label that reads “LT WT 60,000 LBS.” This means the tare weight of the boxcar is 60,000 pounds.
If the tare weight is not marked on the car, you may be able to find it in the train car’s documentation or from the manufacturer.
7.3. Determining the Load Limit
The load limit of a train car is also usually marked on the car itself. Look for a label or plate that indicates the “LD LMT” (load limit) or “CAPY” (capacity). This value represents the maximum weight of cargo that the car is designed to carry.
- Example: The same boxcar has a label that reads “LD LMT 200,000 LBS.” This means the load limit of the boxcar is 200,000 pounds.
7.4. Calculating the Gross Weight
To calculate the gross weight of a train car, simply add the tare weight and the weight of the cargo.
-
Formula: Gross Weight = Tare Weight + Cargo Weight
-
Example: The boxcar with a tare weight of 60,000 pounds is loaded with 150,000 pounds of cargo. The gross weight of the car is:
Gross Weight = 60,000 LBS + 150,000 LBS = 210,000 LBS
7.5. Checking Axle Load
It’s important to ensure that the axle load does not exceed regulatory limits. To calculate the axle load, divide the gross weight by the number of axles on the train car.
-
Formula: Axle Load = Gross Weight / Number of Axles
-
Example: The boxcar with a gross weight of 210,000 pounds has four axles. The axle load is:
Axle Load = 210,000 LBS / 4 = 52,500 LBS per axle
Ensure that this value is within the allowable limit for the tracks and bridges on the intended route.
7.6. Considerations and Best Practices
- Accuracy: Use accurate scales to weigh cargo and train cars.
- Documentation: Keep detailed records of tare weights, cargo weights, and gross weights for all train cars.
- Compliance: Ensure compliance with all applicable regulations and standards related to train car weight.
- Load Distribution: Distribute cargo evenly within the train car to minimize stress on the structure and ensure stability.
By following these steps and best practices, you can accurately calculate the weight of a train car and ensure safe and efficient rail operations. For more detailed information and expert advice, visit CARS.EDU.VN.
8. Real-World Examples of Train Car Weights and Capacities
To further illustrate the concepts discussed, this section provides real-world examples of train car weights and capacities. These examples showcase the diversity of train car types and their varying weight characteristics.
8.1. Example 1: Modern Boxcar
- Type: 60-foot High-Roof Boxcar
- Tare Weight: 65,000 pounds (32.5 tons)
- Load Limit: 220,000 pounds (110 tons)
- Gross Weight: 285,000 pounds (142.5 tons)
- Axles: Four
- Axle Load: 71,250 pounds per axle
- Typical Cargo: Paper, packaged goods, consumer products
- Application: General freight transport across North America
8.2. Example 2: Tank Car
- Type: 20,000-Gallon Tank Car
- Tare Weight: 75,000 pounds (37.5 tons)
- Load Limit: 186,000 pounds (93 tons)
- Gross Weight: 261,000 pounds (130.5 tons)
- Axles: Four
- Axle Load: 65,250 pounds per axle
- Typical Cargo: Ethanol, crude oil, chemicals
- Application: Transport of liquids and gases across North America
8.3. Example 3: Hopper Car
- Type: Open-Top Hopper Car
- Tare Weight: 55,000 pounds (27.5 tons)
- Load Limit: 228,000 pounds (114 tons)
- Gross Weight: 283,000 pounds (141.5 tons)
- Axles: Four
- Axle Load: 70,750 pounds per axle
- Typical Cargo: Coal, grain, aggregates
- Application: Transport of bulk commodities
8.4. Example 4: Flatcar
- Type: 89-foot Flatcar
- Tare Weight: 60,000 pounds (30 tons)
- Load Limit: 206,000 pounds (103 tons)
- Gross Weight: 266,000 pounds (133 tons)
- Axles: Four
- Axle Load: 66,500 pounds per axle
- Typical Cargo: Machinery, steel products, oversized equipment
- Application: Transport of large and heavy items
8.5. Example 5: Autorack
- Type: Enclosed Autorack
- Tare Weight: 80,000 pounds (40 tons)
- Load Limit: 146,000 pounds (73 tons)
- Gross Weight: 226,000 pounds (113 tons)
- Axles: Six
- Axle Load: 37,667 pounds per axle
- Typical Cargo: Automobiles, trucks, vans
- Application: Transport of vehicles
These examples illustrate the wide range of train car weights and capacities used in modern rail transport. Understanding these variations is crucial for optimizing operations and ensuring safety. Visit CARS.EDU.VN for more detailed information and expert insights.
9. The Future of Train Car Weight Management
As the rail industry continues to evolve, advancements in technology and design are driving the future of train car weight management. This section explores the key trends and innovations that will shape the way train car weight is managed in the years to come.
9.1. Advanced Materials and Lightweighting
- Increased Use of Composites: Composite materials, such as carbon fiber reinforced polymers (CFRP), offer significant weight reduction potential and will be increasingly used in train car construction.
- Aluminum Alloys: Aluminum alloys will continue to replace steel in many applications, further reducing weight and improving fuel efficiency.
- Nanomaterials: Nanomaterials offer the potential to create stronger, lighter materials for train car construction, but further research and development are needed to realize their full potential.
9.2. Smart Sensors and Monitoring Systems
- Real-Time Weight Monitoring: Smart sensors will provide real-time data on train car weight, allowing for proactive adjustments to optimize operations and prevent overloads.
- Load Distribution Monitoring: Sensors will monitor load distribution within train cars, ensuring that cargo is evenly distributed to minimize stress on the structure and prevent accidents.
- Predictive Maintenance: Data from sensors will be used to predict maintenance needs, allowing for proactive repairs and reducing downtime.
9.3. Data Analytics and Optimization
- Big Data Analytics: Big data analytics will be used to analyze vast amounts of data from sensors and other sources, identifying trends and patterns that can be used to improve train car weight management.
- Route Optimization: Data analytics will be used to optimize routes based on train car weight, infrastructure conditions, and other factors, reducing fuel consumption and minimizing stress on tracks and bridges.
- Artificial Intelligence (AI): AI algorithms will be used to automate decision-making related to train car weight management, improving efficiency and safety.
9.4. Sustainable Practices
- Lifecycle Assessment: Lifecycle assessment will be used to evaluate the environmental impact of train car materials and designs, promoting the use of sustainable materials and practices.
- Recycling and Reuse: Train car components will be designed for easy recycling and reuse, reducing waste and minimizing the environmental impact of rail transport.
- Energy-Efficient Technologies: Energy-efficient technologies, such as regenerative braking and solar panels, will be integrated into train cars to reduce energy consumption and improve sustainability.
9.5. Regulatory Advancements
- Performance-Based Regulations: Regulations will increasingly focus on performance-based standards, allowing for innovation and flexibility in train car design and weight management.
- Harmonization of Standards: Efforts will continue to harmonize regulations and standards across different countries and regions, promoting interoperability and reducing trade barriers.
- Data-Driven Oversight: Regulatory oversight will be increasingly data-driven, using data from sensors and monitoring systems to ensure compliance and identify potential safety issues.
The future of train car weight management is bright, with advancements in technology and design paving the way for safer, more efficient, and more sustainable rail transport. Stay informed about these exciting developments at CARS.EDU.VN.
10. Finding Reliable Information on Train Car Weights at CARS.EDU.VN
Finding accurate and reliable information about train car weights can be challenging. CARS.EDU.VN is your trusted resource for comprehensive and up-to-date information on this topic. Here’s how CARS.EDU.VN can help you:
10.1. Comprehensive Articles and Guides
- Detailed Information: CARS.EDU.VN provides in-depth articles and guides covering various aspects of train car weights, including types of train cars, factors influencing weight, and calculation methods.
- Expert Insights: Our content is developed by industry experts with years of experience in rail transport, ensuring accuracy and reliability.
- Easy-to-Understand Language: We present complex information in a clear and concise manner, making it accessible to readers of all backgrounds.
10.2. Real-World Examples and Case Studies
- Practical Applications: CARS.EDU.VN features real-world examples and case studies that illustrate the concepts discussed, providing practical insights into train car weight management.
- Industry Best Practices: Learn about industry best practices for optimizing train car weight, improving efficiency, and ensuring safety.
- Success Stories: Discover how organizations have successfully implemented innovative strategies for train car weight management.
10.3. Up-to-Date Regulatory Information
- Compliance Resources: CARS.EDU.VN provides up-to-date information on regulations and standards related to train car weight, helping you stay compliant with industry requirements.
- Regulatory Updates: Stay informed about the latest changes to regulations and standards, ensuring that you are always up-to-date.
- Expert Analysis: Our experts provide analysis of regulatory developments, helping you understand the implications for your operations.
10.4. Interactive Tools and Calculators
- Weight Calculators: Use our interactive weight calculators to quickly and easily calculate the gross weight and axle load of train cars.
- Conversion Tools: Convert between different units of weight (e.g., pounds, kilograms, tons) with our convenient conversion tools.
- Data Visualization: Visualize train car weight data with interactive charts and graphs, gaining valuable insights into trends and patterns.
10.5. Community Forum and Expert Support
- Ask Questions: Connect with other rail transport professionals in our community forum, asking questions and sharing insights.
- Expert Support: Get expert support from our team of rail transport specialists, who can provide guidance and answer your questions.
- Networking Opportunities: Network with industry peers and build valuable connections that can help you advance your career.
10.6. Additional Resources
Address: 456 Auto Drive, Anytown, CA 90210, United States
Whatsapp: +1 555-123-4567
Website: CARS.EDU.VN
CARS.EDU.VN is your one-stop resource for all things related to train car weights and rail transport. Visit us today to access our comprehensive resources and expert support.
This comprehensive guide has explored the multifaceted aspects of train car weight, from the weight of different train car types to the factors that influence their weight, the impact on efficiency and safety, and the innovations driving future advancements. Armed with this knowledge, you can make informed decisions and optimize your rail transport operations for safety and efficiency.
If you’re seeking reliable repair services or want to explore a wide range of vehicles, CARS.EDU.VN is your ultimate destination. We are dedicated to offering trustworthy solutions and expert guidance, ensuring you discover the ideal car and receive top-notch service.
Don’t hesitate! Connect with us today and let cars.edu.vn be your go-to source for all your automotive needs.
FAQ: Train Car Weights
1. How much does a typical freight train car weigh?
The weight varies significantly based on the type of car. An empty boxcar might weigh around 25-30 tons, while a loaded car can weigh 70-100 tons.
2. What factors affect the weight of a train car?
Construction materials (steel, aluminum, composites), car design, load capacity, and added features (braking systems, monitoring equipment) all influence the weight.
3. Why is train car weight important?
Weight affects fuel efficiency, infrastructure maintenance, safety (derailment risk, braking performance), and operational efficiency.
4. How is train car weight calculated?
Gross Weight = Tare Weight (empty car) + Cargo Weight. Axle load is then calculated by dividing the gross weight by the number of axles.
5. Where can I find the weight information for a specific train car?
The tare weight and load limit are usually marked on the car itself. You can also find this information in the train car’s documentation or from the manufacturer.
6. Are there regulations on train car weight?
Yes, organizations like the AAR and FRA set standards and regulations for train car weight to ensure safety and interoperability.
7. How are train car designs evolving to address weight concerns?
Innovations include the use of advanced materials (high-strength steel, aluminum, composites), optimized structural designs, and aerodynamic improvements.
8. What are the environmental benefits of reducing train car weight?
Reducing weight improves fuel efficiency, leading to lower emissions and a smaller carbon footprint.
9. How do smart sensors and monitoring systems help with train car weight management?
These systems provide real-time data on train car weight and load distribution, allowing for proactive adjustments and preventing overloads.
10. What role does data analytics play in train car weight management?
Data analytics can be used to analyze vast amounts of data, identify trends, optimize routes, and improve overall efficiency and safety related to train car weight.